Automation of overhead warehouses for heavy unit loads
Our extensive expertise in transportation, storage, and automation enables us to identify the distinct requirements of each customer and provide comprehensive solutions through the development of turnkey projects for all phases of product movement flow.
Automotive
industry
Coils
Assembly
lines
Textile
industry
Bicycles
Logistics & distribution
Infeed
Material reception, either from internal production or external arrival.
Reception of different types of products and references.
Sorting
It can be done automatically via artificial vision, detection sensor systems, chip and barcode reading, among others, or manually.
Traceability monitoring available from the moment the products are sorted.
Storage
Automatic warehouse equipped with different storage conveyor lines. Dynamic product entry and exit, allowing different movements at the same time.
Depending on customer needs and the amount of references, unitary product or batch storage can be done. Traceability of all products within the warehouse.
Indexing
Preparation of a batch of products according to customer needs. Grouping of different references and quantities as required.
Expedition
Exit of the batches prepared in the indexing area at the moment required and in the desired order. Delivery confirmation once over.
Return
Were it necessary, the product can be returned to the initial part of the system or to any point of the process.
Why automate a warehouse?
- Move large amounts of goods
- Higher security for the stored products
- Ease a production process requiring a permanent flow of components
- Dynamic load storage with single badge or sorting
10 advantages of iclotet warehouses
- 1. Unitary loads
- 2. Full traceability
- 3. Time control between processes and productions by work positions
- 4. Loads up to 250 kg
- 5. Permanent warehouse inventory
- 6. Space optimization
- 7. Reduction of forklift processes
- 8. High productivity and availability
- 9. Prodution up to 500 movements/hour
- 10. Historical data collection and forecasts statistics
ASRS warehouse for tires
Lorem fistrum por la gloria de mi madre esse jarl aliqua llevame al sircoo. De la pradera ullamco qué dise usteer está la cosa muy malar.
- Storage of tires in unitary loads.
- Automatic sorting according to reference.
- Continuous and simultaneous product movement.
- Dynamic flexibility in stock movement in intralogistics.
- Goods-to-person.
- Reduction of storage area/capacity increase of stock.
- Reduction of time to market: High productivity.
- Scada control.
- Labour savings.
- Elimination of forklifts.
- Load and process safety.
- Tyre rotation system.
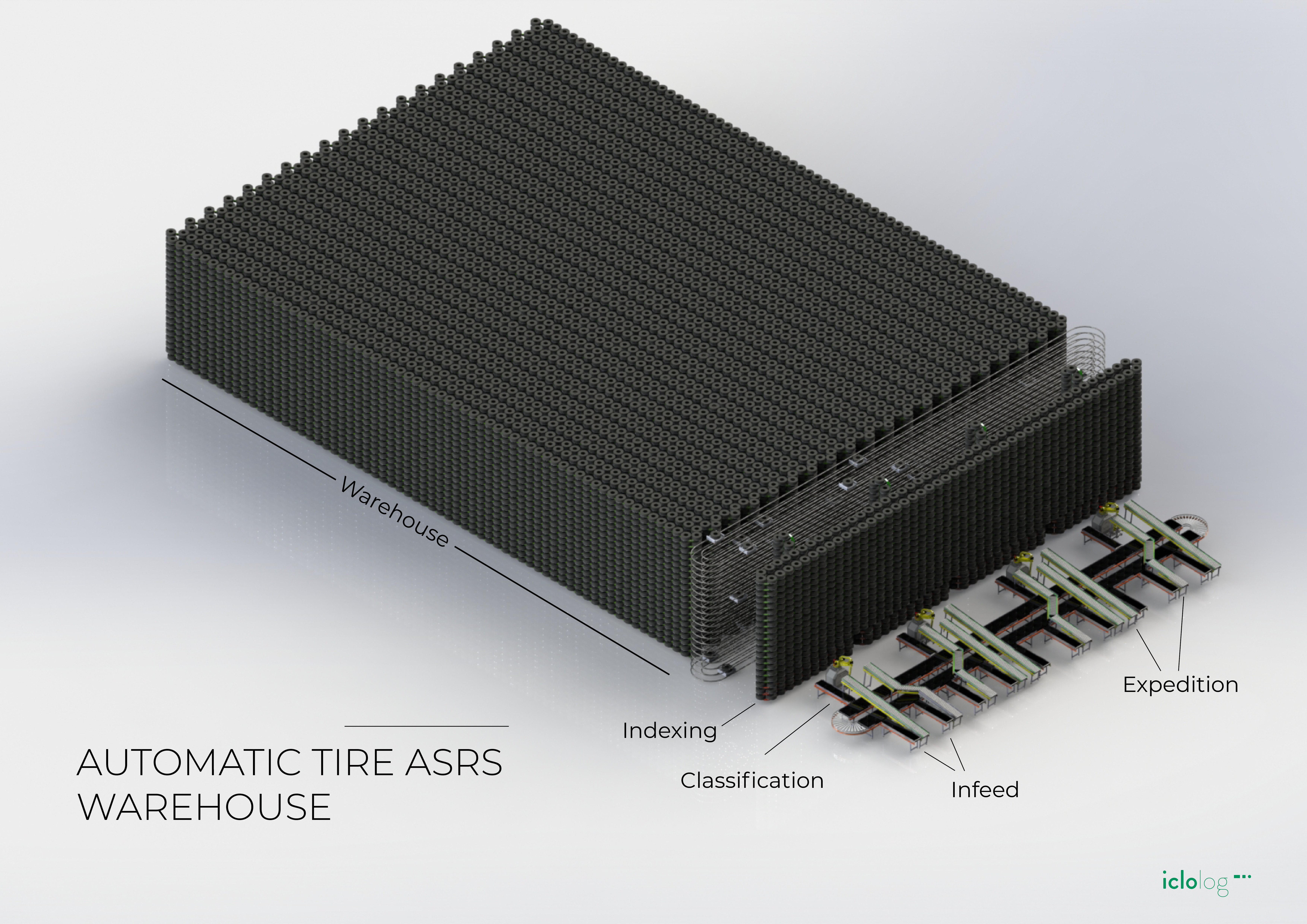
This technology is based on overhead chain conveyors, which allow to manage unitary loads and give dynamic flexibility on intralogistics stok movement. The installation includes two different areas:
1. Tire reception and dispatch area, which includes automatic reference reading and batch preparation. This first area includes 4 processes: Infeed, Classification, Indexing, Dispatching
2. The warehouse is the main part of the installation: Automated warehouse with unit loads and different transport storage lines. It includes dynamic entry and exit of tires allowing different movements simultaneously. It keeps the traceability of each tire, which describes the characteristics of each one.
This technology is based on overhead chain conveyors, which allow to manage unitary loads and give dynamic flexibility on intralogistics stok movement. The installation includes two different areas:
1. Tire reception and dispatch area, which includes automatic reference reading and batch preparation. This first area includes 4 processes: Infeed, Classification, Indexing, Dispatching
2. The warehouse is the main part of the installation:
Automated warehouse with unit loads and different transport storage lines. It includes dynamic entry and exit of tires allowing different movements simultaneously. It keeps the traceability of each tire, which describes the characteristics of each one.